Check out what’s
Trending
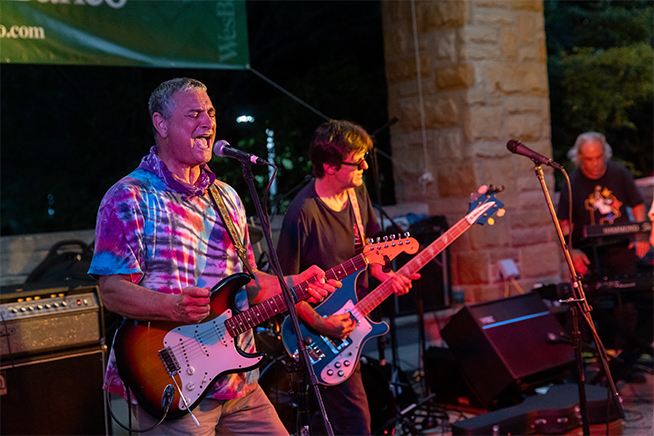
Final Friday summer concerts
Oversight Street maintenance involves Mt. Lebanon’s responsibility to maintain approximately 78 miles of municipal streets and paved alleys, including street resurfacing, joint sealing, brick and concrete roadway repairs and maintenance of guardrails.
Pothole Patching Only emergency repairs of concrete, brick and asphalt streets take place. Municipal crews patch all holes with a year-round maintenance contract covering larger patching. Winter patching with cold material is done on an emergency basis.
Basic Repair Contractual repair of 60,000 square feet (.4 miles) of the most seriously deteriorated streets in the community. This includes work on concrete streets (50 percent) and bituminous streets (50 percent). Concrete slabs are replaced and three-inch bituminous overlay is applied. Municipal crews repair signs and guardrails, and do minor asphalt repairs.
Systematic Repair Additional streets in need of repair are serviced by contract on a systematic basis, with those in the worst condition given priority. About 90,000 additional square feet (.6 miles) of concrete and bituminous streets are repaired, continuing the percentage breakdown established for the basic repair.
Street Crack Repairs Provides for the contract sealing or repair of about 18,000 linear feet of street cracks throughout Mt. Lebanon. Cracks range up to 1/4 of an inch in width, 80 percent of which are normally less than 12 feet long.
Increased Repair Increases contract repairs by about 60,000 square feet (.4 miles) of concrete and bituminous street. The breakdown continues at 50 percent for concrete streets, 50 percent for bituminous. Permits the municipality to reduce the reconstruction frequency from once every 20 years to once every 25 years.
The purpose of a pavement management system is to recommend the most cost effective treatments for our pavements and schedule their applications at the most beneficial time. In other words, our goal is to get the most bang out of our pavement, maintenance and rehabilitation buck.
The Municipality invested in the PavementView module of Cartegraph in 2004 for their pavement management system. A few of the key features/ benefits of this program was that it provided a mechanism with which the Municipality was able to: 1) Assess the current status of its pavement infrastructure, 2) Develop a budget to ensure that the pavement is maintained at an acceptable operating level, 3) Provide recommendations for maintenance and reconstruction roadways on a yearly basis. In 2004, available computer programs that provided these services and detailed analysis for pavement infrastructure management were limited.
As we entered 2020, there were more choices available to engineers and communities alike that can better and more easily address pavement infrastructure management needs. Based on research and testing, the StreetSaver Pavement Management Software was adopted in place of the previous Cartegraph module to manage the annual pavement program in Mt. Lebanon.
At the heart of a Pavement Management Systems (PMA) is the infrastructure database which is the storehouse for all pavement related information collected. Every piece of information in the database is referenced to a particular segment of pavement which it describes. The information stored for each road segment includes street measurements, pavement type (Brick, Concrete, Full Depth Asphalt, etc.), the functional classification (Collector, Local, Cul-de-Sac or Alley), original construction date, maintenance activities, inspections, curb type, etc. Streetsaver then uses this information and applies a degradation curve from these known points to estimate a current Pavement Condition Index (PCI).
The software rates each segment of the 88.2 miles of roadway within the Municipality with a Pavement Condition Index (PCI) number. The number is based on field inspections to determine the defects within the segment, the type of roadway (Brick, Concrete, Full Depth Asphalt, etc.), the classification of roadway (Collector, Local, Cul-de-Sac or Alley) and a known degradation based upon age. The PCI allows for a comparison of all the segments and their ranking to optimize Road Programs within the approved budget. In 2021, the roadways were reevaluated to align the degradation curves with the current roadway conditions. The following table gives the PCI range and corresponding roadway status.
PCI Range | Roadway Status |
---|---|
85-100 | Excellent |
65-84 | Acceptable |
45-64 | Marginal |
0-44 | Failed |
Step 1 — Replacing deteriorated curb can take two weeks or more, depending on the weather. New curb is poured and covered with a curing compound to retain moisture and slow the drying process; the longer the curb “cures,” the stronger it will be. A sealing compound is then applied to the curb and sidewalk to prevent deterioration from road salt. If grass, sidewalks or driveways close to the curb are damaged, they will be repaired before the project is considered complete. The contractor will tell you in advance if and when you need to move your car.
Step 2 — Some storm and sanitary sewers, manholes and utilities may be reconstructed during curb and street reconstruction.
Step 3 — Utility companies will replace gas and water lines under the street as necessary. This reduces the chance of needing to re-open the new street for repairs in the near future.
Step 4 — After the curb is replaced and repaired, the old surface and base will be removed. The excavation could be as deep as 18 inches. The contractor will try to excavate in a way that minimizes the disruption of vehicle access. However, once the existing asphalt, brick or concrete surface is removed from your street and the sub-grade is exposed you will not be able to access your driveway. The curb will also be exposed and at this time will be painted with a waterproofing material. Care should be taken to avoid contact with this material.
If necessary, a sub drain will be installed next to the curb (or where a new curb is installed, the drains will be installed with the curb). This drain will intercept subsurface water, carrying it to the nearest storm sewer and prevent moisture from reaching the street base. This process could take at least two weeks, depending on the weather and how long it takes the utility companies to finish Step 3.
Step 5 — Contractors will inspect the exposed sub-grade and decide what areas need replacing. After these areas are repaired, a stabilizing fabric will be applied to the sub-grade, a 6-inch layer of aggregate base will be placed on top of the fabric, and the street will be graded to provide a crown in the center that will help with drainage. Then, a bituminous base will be placed on top of the aggregate base.
Step 6 — The final bituminous binder / wearing surfaces will be applied in two layers, each 1-1⁄2 inch thick. To keep out moisture, a hot bituminous seal is applied to the joints where the surface meets the curb. You will not be able to drive on your street for at least three days. The contractor will notify you about 12 hours before beginning this process.
Finally, any disturbed grass areas will be replaced with topsoil, seeded, fertilized and given a heavy soaking of water. From that point on, we ask your cooperation in watering and maintaining the area as you would any newly planted area.
There will be times that no one is working on your street, either because of the phasing of your project or reconstruction work being done by the contractor on other streets in Mt. Lebanon. Be assured that the contractor for the project has developed a tentative schedule and will complete the work as quickly as possible. The actual duration will depend on such things as weather, conditions encountered and the number of utility lines that need replacing. Construction workers are not familiar with the schedule and may not perform any work not specified by their contract with the Municipality of Mt. Lebanon.
Here are a few tips that can stretch the tax dollar, keep your streets looking good and help the project
conclude safely.
Check out what’s
Final Friday summer concerts